Packaging machine repair service for cost-effective maintenance solutions.
Exactly How Expert Packaging Machine Repair Work Services Lessen Downtime and Boost Efficiency
Expert product packaging machine repair work solutions are crucial in lessening downtime and enhancing performance through specialized diagnostics and timely treatments. The ramifications of such services expand beyond instant repair services-- unpacking the wider effect on functional performance reveals crucial understandings into long-term productivity strategies - packaging machine repair service.
Importance of Timely Repair Works
Prompt repairs of packaging machines are essential for preserving operational performance in any manufacturing environment. When machinery malfunctions or breaks down, it can cause significant disruptions in assembly line, leading to boosted downtime and lost income. The longer a product packaging machine continues to be out of payment, the higher the effect on overall productivity, possibly creating delays in satisfying orders and diminishing customer complete satisfaction.
Along with the immediate financial ramifications, postponed fixings can bring about much more comprehensive damages to the equipment. Components that are not attended to promptly can weaken even more, calling for more expensive repair services or full substitutes, which might have been avoided with timely intervention. Moreover, normal maintenance and prompt repair work can improve the life-span of packaging machines, guaranteeing that they run at optimal performance degrees.
Purchasing specialist product packaging equipment repair services is crucial for minimizing these threats. A proactive approach to repair work not just maintains production routines however also promotes a society of dependability within the company. By prioritizing prompt fixings, services can keep their affordable edge, maximize resource allowance, and eventually enhance their lower line through boosted functional efficiency.
Know-how in Diagnostics

Effective diagnostics not only promote speedy recognition of troubles yet likewise improve the overall integrity of product packaging procedures. By carrying out comprehensive assessments, technicians can examine the health of critical components, guaranteeing that even minor irregularities are dealt with immediately. This interest to information decreases the risk of unexpected break downs, which can cause costly downtime.
In addition, specialist diagnostics offer important insights right into functional patterns, permitting organizations to make enlightened decisions pertaining to tools upgrades or alterations. By leveraging these understandings, companies can optimize their product packaging processes, causing enhanced efficiency and performance. Ultimately, purchasing diagnostic expertise is necessary for organizations seeking to maintain seamless procedures and support high requirements of high quality in their product packaging processes.
Preventive Maintenance Conveniences
Preventative upkeep complements specialist diagnostics by proactively resolving potential concerns prior to they show up into severe issues. By implementing an organized preventative maintenance program, companies can substantially decrease the threat of unforeseen machine failings, thus decreasing pricey downtime. Normal assessments, cleansing, and components substitute aid guarantee that product packaging machinery runs at optimum effectiveness.
Among the crucial advantages of preventive upkeep is its capacity to prolong the life expectancy of equipment. By frequently maintaining equipment, businesses can avoid the worsening impacts of damage that usually cause major repair work or replacements. packaging machine repair service. This not only conserves resources yet additionally enhances the total reliability of manufacturing processes
Furthermore, precautionary maintenance adds to improved security conditions within the office. By identifying and correcting prospective threats prior to they intensify, companies develop a much safer atmosphere for their staff members. This proactive strategy not only secures workers however likewise cultivates a society of duty and watchfulness.
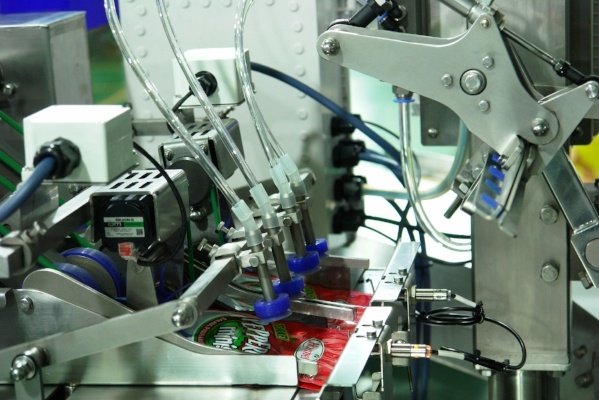
Custom-made Service Solutions
Recognizing the one-of-a-kind requirements of each business, personalized service remedies for product packaging equipment repair work deal customized methods that enhance functional effectiveness. These options are created to resolve details challenges dealt with by different sectors, making certain that machine downtime is lessened and efficiency is taken full advantage of.
Expert repair services start with a comprehensive analysis of a company's product packaging procedures. By recognizing the certain machinery included and the demands of the production environment, specialists can establish an individualized repair and maintenance strategy. This might consist of specialized training for internal personnel, the execution of predictive maintenance innovations, or the stipulation of specialized support throughout height production times.
Moreover, personalized solutions can integrate flexible solution arrangements that straighten with a company's operational routine, enabling see this here repair services to be performed throughout off-peak hours. By focusing on the distinct requirements of each company, these bespoke solutions guarantee that repair work are not just efficient yet likewise seamlessly incorporate into existing workflows.
Eventually, the emphasis on personalization makes it possible for companies to maximize their product packaging processes, resulting in improved reliability and efficiency of equipment, which is important for preserving affordable advantage in today's fast-paced market.
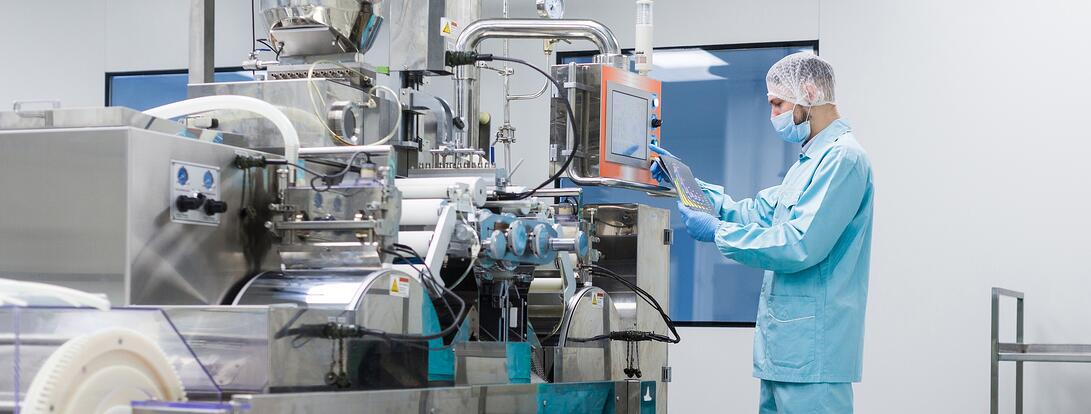
Effect On General Effectiveness
Custom-made service remedies not just address particular fixing needs however additionally play a considerable duty in boosting general operational effectiveness. By offering targeted treatments, specialist product packaging machine repair service solutions directly lower the frequency and period of equipment failures. This positive approach ensures that production lines remain operational, minimizing interruptions that can cause pricey downtime.
Furthermore, effective fixing services add to smoother process, as well-maintained equipment runs at ideal efficiency degrees. When makers work properly, the high quality of packaged items boosts, resulting in fewer issues and much less rework. This improvement not only enhances efficiency however additionally strengthens customer fulfillment.
Furthermore, regular upkeep and quick action times from fixing experts promote a culture of reliability within the company. Employees can concentrate on their key tasks rather than bothering with possible my sources devices malfunctions. As a result, the overall throughput of the production process increases, enabling companies to satisfy need extra efficiently.
Eventually, the critical investment in expert repair work services converts to boosted effectiveness throughout all functional aspects, making sure that services can adapt and grow in an open market. This synergy in between maintenance and productivity is essential for lasting success.
Verdict
In conclusion, expert packaging device repair work services play a vital duty in decreasing downtime and boosting performance within producing settings. Prompt repair services, specialist diagnostics, and preventive maintenance contribute to the integrity of devices, while personalized service solutions deal with certain functional demands - packaging machine repair service.